8月13日,吉利汽车邀请媒体探访义乌动力基地。据介绍,该基地成立于2014年6月,是集发动机研发、制造为一体的实力型制造企业。基地总投资75亿元、规划年产能120万台发动机,主要生产1.0TD发动机、与沃尔沃共同研发的1.5TD发动机和沃尔沃主导研发的2.0TD发动机。据悉,义乌动力基地是吉利动力总成系统九大生产制造基地之一,是全球最大的高端动力智能制造基地,同时也是世界级的微米工厂,全面对标欧洲豪华车标准。
♦微米工厂名不虚传
吉利借助集团全球供应链优势,通过联合采购世界最顶尖的高精密智能制造装备、检测仪器等打造的“微米工厂”,来确保产品高精度、高品质、高一致性,实现欧洲豪华车动力制造标准。之所以称之为微米工厂主要是因为:
第一、该基地实现了0-5微米的智能制造精度。制造基地缸体线、缸盖线采用国际顶尖GROB最新一代双主轴卧式加工中心,可以实现在线实时监控、调整加工精度,在线自动测量对比,可以根据加工过程中,发动机缸体、曲轴、缸盖的热胀冷缩情况,在线自动测量对比,并进行补偿加工,补偿精度范围精确至0-5微米,并通过每一个零件的独有身份证,精确记录制造精度。
第二、该基地拥有1微米分组“零失误”智能选配系统。发动机核心部件的曲轴孔、曲轴、曲轴瓦,在制造过程中会根据各自身份证记录的制造精度,按照每1微米分为一个组别,比行业2微米的标准高出50%。在内装线上,通过二维码身份识别,自动识别缸体曲轴孔和曲轴主轴颈的配对关系,保证每一台下线的发动机的曲轴孔、主轴承瓦和曲轴、连杆孔、连杆瓦和连杆颈之间间隙,满足微米级设计标准。
第三、0.5微米级的超级三坐标检测。基地检测设备采用蔡司、马尔、埃迪科世界顶级供应商,其中精密测量室负责品质抽检的终极“BOSS”是拥有“计量检测高级研究员”水准的超高精度三坐标测量仪,检测精度高达0.5微米,从而保证万台如一的一致性。
♦自动化智能化程度高
义乌基地全面采用沃尔沃工厂标准,引进世界顶尖级的先进高端智能设备来生产制造精品发动机,智能化程度很高,记者在工厂内参观时,看到很多全自动的智能化设备,并且在道技场亲身体验了多个自动化辅助设备,例如ATLAS拧紧设备。例如装配线使用ABB机器人、ATLAS拧紧设备、自动涂胶测试等自动化设备,涂胶工位采用可以自动检测涂胶精度的国际知名品牌Cognex的摄像系统,关键螺栓拧紧工位采用全自动设备拧紧,前后油封压装采用伺服电缸压装,整条装配线三分之一工位为全自动无人工位,完全代替了人工及传统的设备搬运模式。机加线采用柔性生产工艺,引进德国进口珩磨机、高压清洗机、高速数控加工中心和多条自动线,采用自动上下件、自动输送、高压去毛刺、真空干燥、冷却等先进工艺,设备精度和生产制造工艺均达到行业先进水平。
♦安全、环保、节能的制造工厂
除了在制造方面精益求精以外,义乌动力基地还秉承安全、环保、节能的生态制造理念,全力打造绿色工厂。主要表现在三方面,首先是绿化率40%以上,整体绿化面积达到150000㎡ ,绿化率达到40%以上,比绿色小区更高10%,节能、环保,打造对大自然最友好的绿色动力小镇。其次,空气负荷最小化。53套加工设备100%配套世界先进的油雾净化处理系统,净化油雾、颗粒物等污染因子,净化率达到95%以上,通过高于外部空气的气压,形成负压生产环境,保证车间整体环境不受污染。同时,基地气体实际排放数据0.5mg/m³,比国家标准规定的120mg/m³高了240倍,将智能制造对空气环境的负荷降到最低水平。第三,用水负荷最小化:基地生产用水循环方面,采用业内一流的减压蒸馏设备进行蒸馏浓缩,蒸馏效率达到90%以上,蒸馏水比国家回用水标准高两倍,回用于现场清洗机,实现废水“零排放”,每年能节约6000吨的工业用水。
编辑:刘晓烨

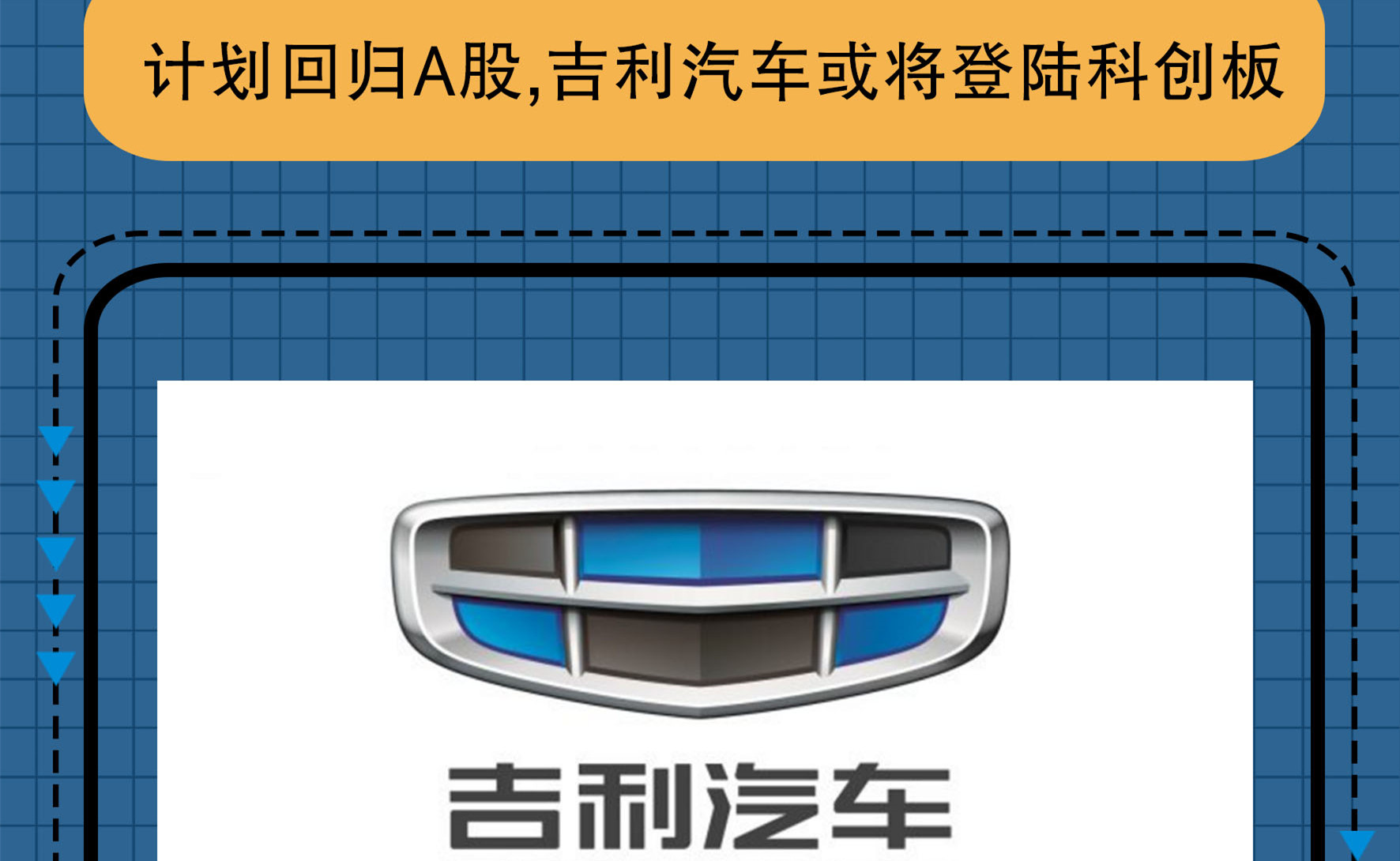
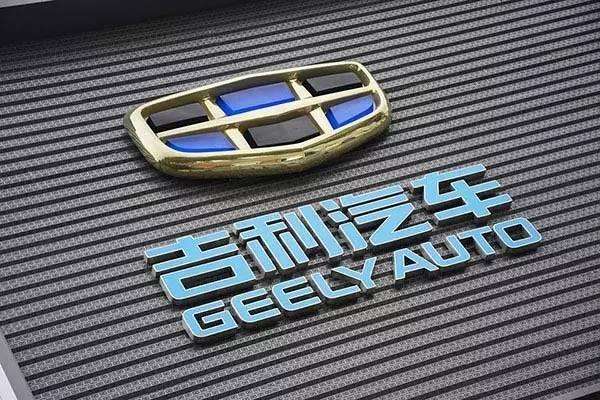
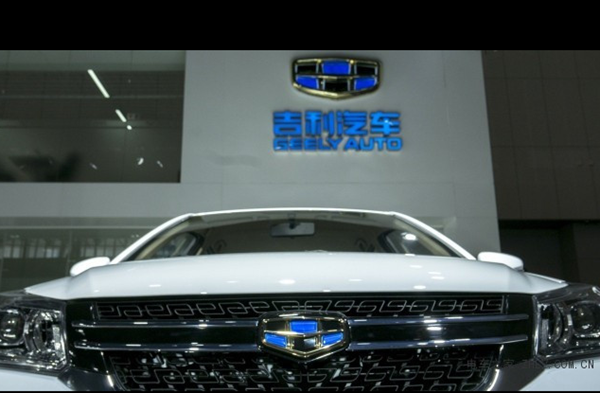
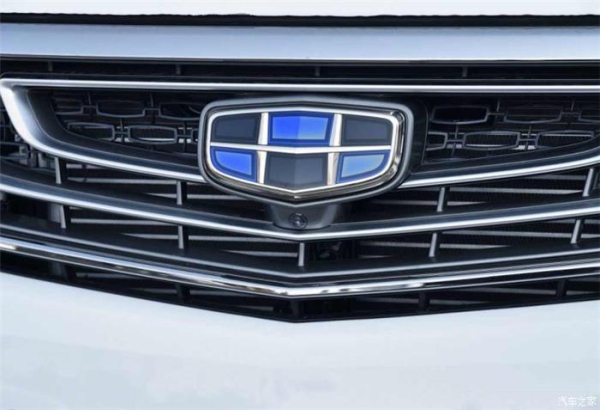
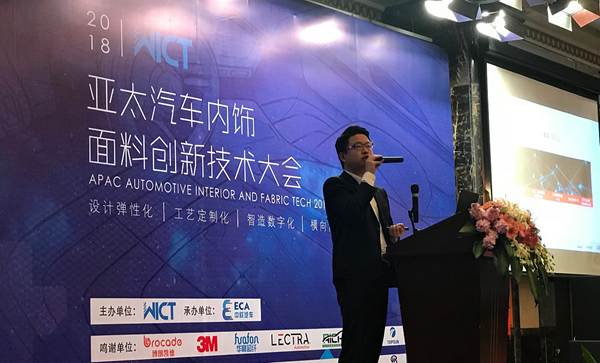
