面对全球汽车产业电气化、智能化、网联化变革提速,国内汽车零部件企业应牢牢把握技术升级趋势,聚力实现核心技术自主可控,引导整零协同配套关系,实现新形势下的高质量发展。
紧紧把握零部件技术升级趋势
伴随汽车产业技术和产品迭代频率加快以及跨领域交叉融合,新能源汽车零部件正在向多功能集成化、“专特新”个性化、机电液(气)一体化方向持续升级。
1.多功能集成化
以动力总成、底盘系统为例,单纯的机械装置、电器模块等已经难以满足新能源汽车日益丰富的功能需求。在节能汽车领域,为进一步降低整车油耗,AMT等自动变速器已升级成集成式传动装置,集控制器、逆变器、电动机、变速器、缓速器、取力器等诸多功能于一体,并将在今后10年乃至更长时间成为混合动力汽车的核心配置。在新能源汽车领域,美国艾里逊最近推出的中重型电驱动桥以多功能集成化为特色,通过高低挡AMT变速器和双直驱电机的配置,以及驱动桥TCU和电池BMS通讯,可为驱动桥提供合适的即时扭矩动力;同时,通过取消主被动盆角齿轮、传动轴、主减速器,进一步提升产品集成度。在智能网联汽车领域,以ABS为代表的紧急制动系统通过智能化升级,已经成为ADAS系统和整车能量回收系统的重要组成部分,以线控制动为导向的前瞻技术也在加速落地。
汽车零部件企业要围绕近期、中期、远期新能源汽车的发展趋势,结合自身产品现状,制定企业近中远期的新产品研发重点,发展多功能集成化的产品。
2.“专特新”个性化
随着新能源汽车的快速发展,尤其在目前各汽车制造企业竞争激烈的情况下,满足细分市场的个性化需求也成为未来竞争的焦点。尤其在一些具体场景,根据里程、路况、负荷等最大限度地发挥新能源汽车的节电降耗性能,需要匹配最佳的电池电量,定制特殊配置车辆,局部采用轻量化设计,来满足特定场景下的使用要求。
另外,新能源汽车的技术路线尚未达成统一,多元化动力仍将在较长时间内并存发展。对于汽车零部件企业而言,面对不确定性需求下的技术升级和产品换代,需要进一步加强同整车企业的密切配合和同步开发,通过提升自身的专业能力和研究水平,及时提供相适应的先进设计。
目前由于信息通讯的发达,以及各类设计软件的应用,包括仿真模拟、3D打印、有限元计算等研发手段和措施,大大缩短了零部件产品试制试验的时间和过程。但这些软件需要高水平的研发人员根据应用场景、材料设备和各种工况进行改进、提升和完善,光有先进的软件,没有合适的研发人员有效熟练地操作使用是不行的。尤其在“专特新”方面,对技术研发人员的水平要求更高,对研发设施和手段也要求更完善。这正是零部件企业在产业变革趋势下,能否快速发展甚至是决定企业成败的最关键要素。
3.机电液(气)一体化
汽车零部件集硬件载体和软件控制于一体,机电液(气)一体化的持续升级是必然趋势。从产业链配套体系优化角度来看,整车企业将更加注重整体架构和差异化功能的建设,通用化、模块化的总成类部件将交由零部件企业来完成,这对配套商能否系统性地提供机电液(气)一体化系列产品提出了更高要求。以法士特为例,通过抢抓机遇,由单一的、传统的手动机械变速器生产厂家,变成了一家拥有诸多机电液一体化产品的企业,能够为新能源汽车提供相应的智能传动装置。
同时,随着汽车电子化步伐的加快,整车集成的控制器已由2000年的个位数激增至当前的100多个,但是由于各独立控制器对操作系统的需求差别很大,难以实现数据互通或功能整合。因此,将变速器、离合器、缓速器、取力器、制动系统等总成的电子控制模块集成在一起,才能有效为整车企业的车辆系统控制器(VCU)提供适配好的“域”控制器。在助力整车企业缩短研发新车时间的同时,巩固整零战略合作关系。
加速转型适应新型整零合作关系
零部件企业除了要充分把握新能源汽车技术发展趋势以外,在全球范围内,也应随时关注新能源汽车整零合作关系。一般情况下,整零合作关系可以从资金合作、生产技术和管理、企业人员交流、整零配套关系等几个层面来进行分析与判断。
从双方资金层面看,欧美模式是整零双方各自独立;日本模式主要是整车企业对一些主要关键零部件厂进行投资;中国模式则呈现多元化投资格局。
从生产与管理技术层面看,欧美模式中,零部件企业有较强的产品研发能力,在技术交流上处于主动地位(例如博世、采埃孚ZF、德尔福等),各大汽车公司将零部件企业的生产管理系统纳入自己的系统中。日本模式主要由整车企业派人对零部件企业进行技术指导,在技术交流上处于主动地位。中国模式下,同一系统内的零部件企业与整车企业合作比较密切,接受整车企业的指导;但其他类型的零部件企业与整车企业之间的合作和交流相对较少。
从双方企业人员业务交流情况看,过去欧美整零企业交流十分有限,现在整车企业已开始接受零部件企业的技术人员参加新车型开发计划,还向零部件企业派驻现场代表等。日本模式双方交流较多,一直是整车企业派遣技术、管理人员到零部件企业指导,零部件企业的技术人员也可以到整车企业参与新车型的开发。而在中国,整车企业与零部件企业的人员业务交流大多尚未形成制度,只是在必要时进行交流和沟通,计划性和周期性较差。
从配套关系看,欧美模式主要是依靠合同、契约来维系整零双方关系;日本模式除了用资产、契约维系双方关系外,还依靠各种协会维系,整零双方是既竞争又合作的关系;中国模式正在由传统的自然紧密型关系(有一定排他性)向制度化、规范化方向发展。
新能源汽车和传统汽车有很多不同之处,甚至有的是颠覆性差别,最大的区别是机械装置应用越来越简单、电子应用却越来越多,因而对专业的深度、广度要求也越来越高。鉴于这些质的不同,零部件企业的转型升级更为迫切,因为包括产品技术、制造设备、工程技术人员的现状和未来,都和当前有巨大差别。零部件企业应有更强的危机意识,迅速响应产业趋势变化,积极采取应对措施,才能适应新能源汽车发展形势下的转型升级。
聚力实现关键技术自主可控
当前,供应链自主可控已成为行业共识。据商务部统计,近年中国汽车零部件行业外资/合资厂商数量仅占20%,而营业收入却占全行业约80%;尤其汽车电子和发动机关键零部件等高科技含量领域,外资市场份额达到90%。在中国汽车工业协会统计的我国规模以上1万多家汽车零部件供应商中,进入全球汽车零部件供应商百强的仅有6家。自主零部件还相对落后,具备较大成长空间,尤其是在以下领域需加快技术研发的步伐。
1.车规级芯片
芯片之痛,不仅刺痛了华为、刺痛了中国,也刺痛了世界上很多国家。当前,我国产业界面临的主要问题并不是很多先进制造产品优不优的问题,而是有没有的问题。比如荷兰ASML光刻机的很多关键核心零部件由欧美日制造,却对我国禁售,导致我国无法制造出高精度光刻机。中科院被迫走了另外一条技术路线,欲突破西方光刻机的封锁。同理,在很多先进技术被封锁的情况下,我们必须要努力攻克。
2.动力电池
虽然我国已经拥有了全球第一的动力电池产能,也拥有了宁德时代、比亚迪等世界级的动力电池企业,但大部分动力电池企业技术仍相对落后,很多产能还需进行技术升级和品质提升。在关键技术上,应该着重在长续驶里程、高安全、全气候动力电池,固态电池,以及高比能正负极材料、耐高温隔膜、耐高压阻燃电解液等方面进行技术攻关。此外,在动力电池回收利用的效率和效益上也应该加大攻关力度。
3.电驱动系统
我国车用电驱动系统虽然在性能指标参数上与世界先进水平基本持平,但在生产自动化和智能化上投入相对较少,导致产品一致性与国外企业仍有差距。此外,我国电机高性能材料以及电驱动控制系统的功率器件等依赖国外进口,电驱动产品的集成化能力仍需改善。下一步重点攻关的技术方向是高集成电驱动系统,高功率、高密度驱动电机与电机控制器等。
4.车联网
在《国家智能汽车发展战略》的指引下,我国车联网技术发展迅速,单车智能和车路协同同步发展,车联网测试示范区和标准法规建设同步推动,汽车产业与交通、信息和ICT等产业加速融合。不过,仍然有很多技术和产品亟待突破,下一步应重点攻关激光雷达、车载操作系统、车载计算单元、线控制动和转向等核心技术与产品。
5.氢燃料
国家正在积极推动氢燃料汽车示范城市群的建设,北京、上海、广州等地在氢燃料汽车的开发与示范推广上已积累了一定经验,基本形成了从整车到燃料电池系统到核心关键零部件的领军型创新型企业。下一步除了要在加氢基础设施的建设和管理上下功夫以外,还要加大针对高功率、低成本、高可靠性燃料电池堆,高性能膜电极、高集成氢气循环泵、70MPa高压储氢瓶等关键核心部件的产业化攻关。
6.充换电设施
充电基础设施建设对于加速电动汽车推广至关重要。在现有交流慢充和直流快充的基础上,我国产业链企业应该加大对智能有序充电、大功率充电、无线充电和快速换电等先进技术的研发和突破,以应对未来我国新能源汽车的爆发式增长和充电便利性的差异化需求。
综上所述,中国汽车行业和零部件企业责任重大,要争分夺秒抓紧排除有可能“卡脖子”的危险。有压力才有动力,有紧迫感、危机感才能发奋创新。
创新、专注助力零部件企业高质量发展
1.持续自主创新
创新,是永恒的主题。如今,汽车除了具备交通工具属性之外,消费者对其功能属性提出越来越高的要求,从而驱动产品技术升级。随着新技术、新工艺、新材料、新场景的发展,无论是创新手段、创新基础还是创新需求等,都在发生巨大变化。没有创新的企业将举步维艰,失去市场和生存的基础。
2.专注细分市场
“一招鲜,吃遍天”的时代已一去不复返了。中国市场大、人口多,各地区的地形地貌、人文风俗、消费习惯各不相同,对汽车产品的需求也不尽相同。零部件企业也需顺应市场要求,积极推出适用的细分产品,满足不同企业、不同产品、不同场景的需要,从而赢得更广阔的发展空间。
(作者系中国汽车工业咨询委员会委员、中国齿轮行业协会名誉会长、陕西法士特集团有限公司原董事长)
编辑:李卿
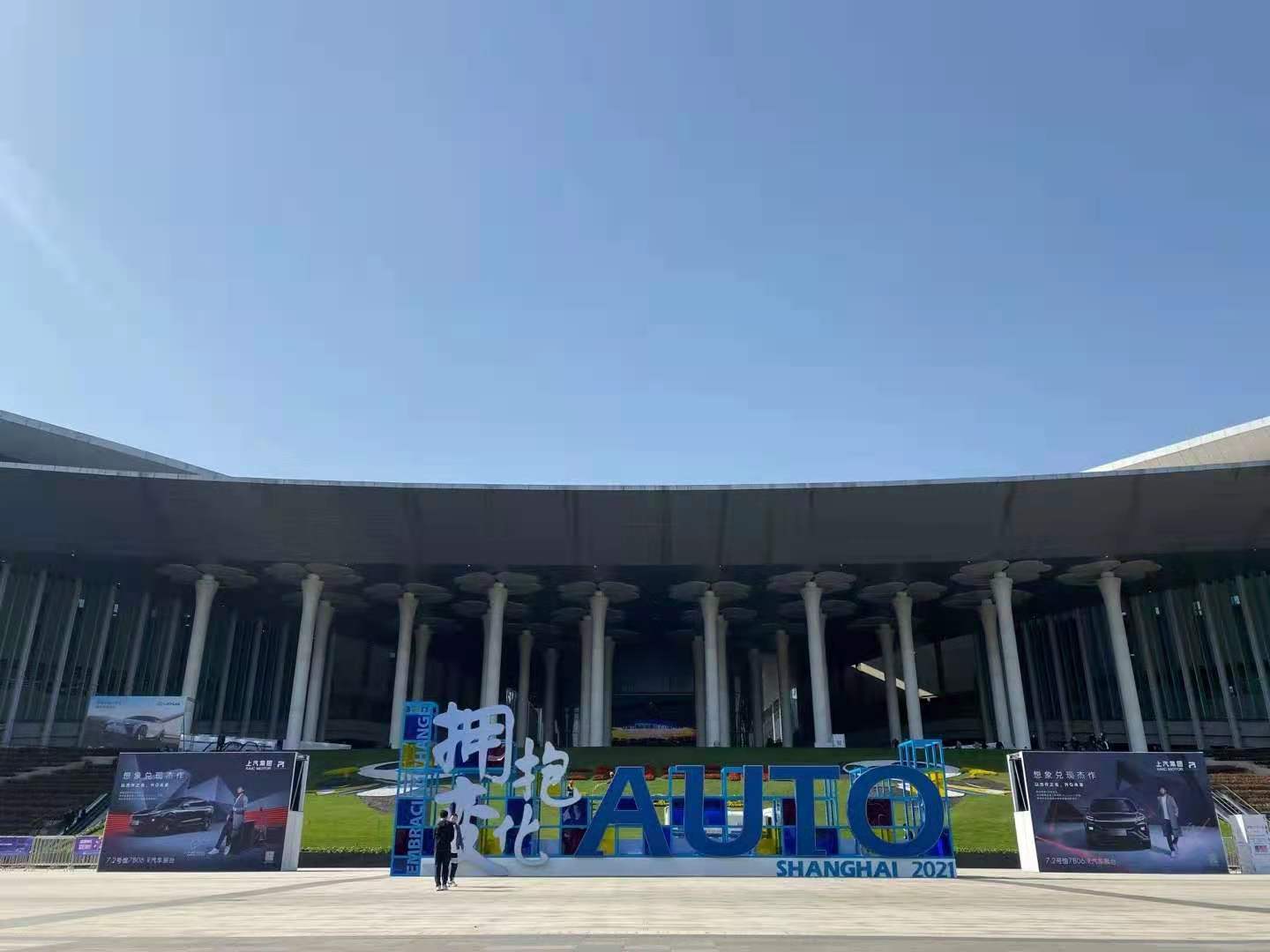
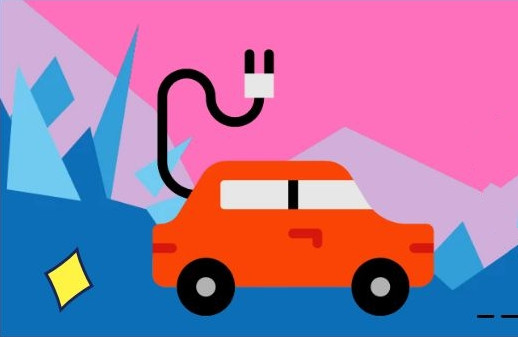
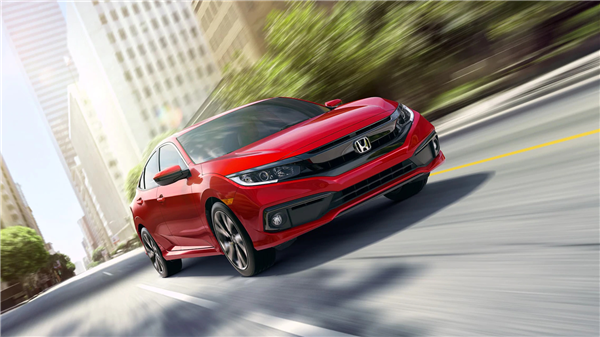
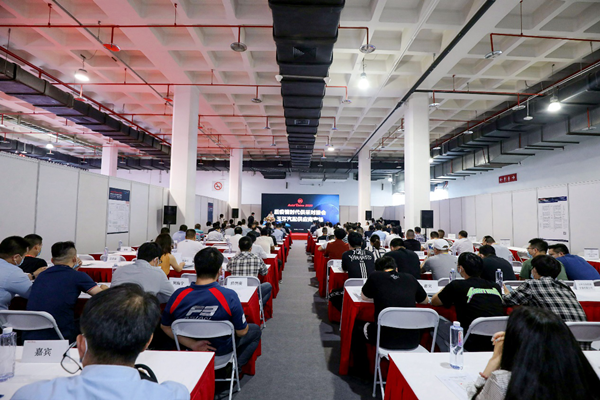
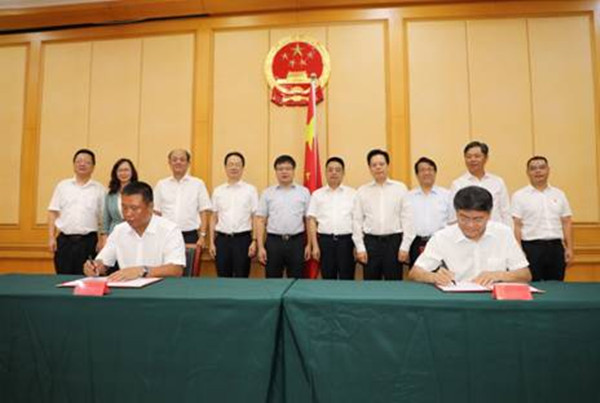
