9月14-16日,由中国汽车工程学会与国际氢能燃料电池协会(筹)共同主办的第五届FCVC大会于上海汽车会展中心召开。同济大学教授张存满到场并发表了主题为“车载储氢技术发展趋势分析”的演讲,以下为文字实录:
关于车载储氢的发展趋势,首先先介绍一下背景,车载储氢分两大类,一种是基于物理态的储氢,一种是材料或者叫化学,实际上化学都是基于材料体系的。
车载储氢里面有几个很重要的要求,第一个一定具备较高的能量密度,第二个是充装的时间,使用要有便捷性,和车不太一样,乘用车三到五分钟稍微快一点,货车、大车基本十五分钟以内完成。
第二个要安全,满足安全性,还有最大的挑战是低成本。对车用要求来讲,基本要满足这四个要求,不论什么技术,这个是DOE和全球整个地方统一下来,这个指标主要是DOE2015年提出来的指标。
下面分成三个部分介绍,第一个整个车载储氢技术,车载储氢类型上分成两大类,第一个是基于物理态,高压、低温,低温液氢加上压缩储氢,第二类基于材料,实际上叫压缩,随着压力的提升密度就上来了,最好的目前是四型瓶到70GP这样一个水平,液氢可以到7.5,只是重量比,压缩是基于液氢低温压缩,不是普通的压缩,低温压缩可以到7.4,能量密度也很高。
物理类的吸附,材料有物理状态,吸附类的,多孔材料就是吸附类,还有基于这个完全是材料偏化学态储氢,金属化合物、DOS其他的化学物质,整个应用来看实际上基本上都是高压,这是70GP高压储氢应用,这是三型瓶、四型瓶,这是35GP,实际上,液氢这块当时宝马推出一款后面液氢车上目前是没有的,但逐渐的可能会有一些商用车,包括国内北汽福田做了一个商用车,也在做一些车的示范和推广。
接下来重点讲几个事情,物理储氢展开,首先要介绍它的高压,高压储氢里面的类型,一型、二型、三型、四型瓶,一型瓶是纯钢,二型瓶是环蚕的,三型瓶是金属内胆,加上碳纤维全缠绕的,四型瓶内胆是塑料的,有机物这种类型,。
高压储氢有什么技术特征包括成本特性,技术这块很快过掉了,全金属的看特征就知道了,目前两个三型瓶成本是一个以100,现在以四型瓶为100基数,相当三型瓶成本是它的两倍,这个是针对70GP的。
三型瓶随着规模的上升可以降一点,但是它仍然是四型瓶的1.5、1.6倍水平,而且四型瓶未来降幅空间还是很大,相当于现在未来四型瓶成本可能到目前三型成本的四分之一,实际上它的下降成本还是比较大的,聚焦到四型瓶特征来看,这两年高压这块比较热,特别是在国内,原来主要在供三型瓶,这两年攻克四型瓶产业化技术特点,四型瓶有一些优点,第一个是轻大家都能想得到,内胆是塑料的所以轻,这是密度,1.4,这个是0.83,这是明显高了。
成本四型瓶是三型瓶未来的二分之一,为什么,技术本身特别造成的,因为内胆本身比较便宜,成形方便。
第二个特征对碳纤维需求量大幅度下降,造成这个优势,四型屏有什么优势,一个轻,但是一个缺点是什么,抗轻的能力,造成内胆失效包括渗透的精密性这是它的挑战,但是它抗疲劳,因为它的弹性能量比较好,塑形变形能力好,所以抗疲劳性能好,成本比较低,安全性没有碎片完全有机的为一体,最大的问题就是氢气的抗渗透能力差,这是一个点,核心是降成本,最重要的优点,低成本、轻量化、安全性好。
简单的介绍一下纤维的缠绕方式,其实核心有三种缠绕方式,一种环向缠绕,一种低角度缠绕,和高角度的缠绕,不同缠绕发挥得强度不一样的,这个环缠走向的夹角,纤维发挥得最好效能,制造压力瓶的时候尽量多用换向缠绕,尽量多用低角度螺旋,这个是高角度螺旋,和上面垂直的,这就是一个缠绕方式变化,经过优化瓶瓶口未知的设计,可以大量的降低我们碳纤维的用量,这就是它的实效的类型,最难的是怕它出现危险,出现爆炸、爆破,出现这个退化,所以说它有损伤失效,失效类型主要有三种,第一个是爆破了,整个强度摔坏了以后爆炸,这是最大的,第二个损伤,包括内部的损伤,还有这个外部的一个损伤,就是外部的划伤、磕伤,内部是内伤。
第三个是它非结构性的退化造成的,还有疲劳,实际上是重点要攻克的地方,这种东西是可以避免的,设计和计算好,尤其是这块,是真正应用里最讨厌的是疲劳失效。
疲劳失效,四型这块大的类型失效还是差不多的,但是四型瓶单独提高,它的失效跟这个不一样,更有独特的地方,第一个是纤维层的损伤,纤维层损伤包括纤维本身强度的衰退,第二个是肌体,主要是树脂和纤维之间的相结合,界面失效,纤维和树脂之间的界面。
第二个内胆的损伤,内胆的损伤包括塑料层本身的损伤,第二是纤维层的起泡,渗透了有时候出不来,最后起泡,起泡渗透量就上来,还有肌体,纤维复合层和内胆纤维失效造成继续坍塌,这是四型瓶失效里非常重要的几种方式。
在整个压力容器的设计里面,首先进行硬力设计计算,还有一个硬力应变,特别对四型瓶来讲,对三型来讲最大的问题就是应变,应变大了容易疲劳开裂,四型瓶重点强调硬力损伤,不同类型里注重点不一样。
接下来讲低温的,低温这块主要是液氢,它的核心四个部分组成一个内胆、支撑体,第二个是绝热层,真空加上里面特殊的包袱绝热,第四层就是外面这个壳,在四型瓶来讲,绝热是关键,但它的系统还是有一定复杂度,它有它的特征,四型瓶有什么问题有什么优点,优点就是密度高,缺点是能耗高,液氢本来液化的损失超过30%以上,国内水平可能损失50%以上,最好达到30%的损耗,本身储氢能量30%用于它的液化,但是它本身储热里绝热不能做到百分之百绝热,罐越小绝热越来越难,所以造成整个储氢的成本实际上是偏高的。
还有一个成本,很重要一点,液氢在车上的挑战是什么,一直要蒸发,不可避免要蒸发,一段时间不用,氢气怎么维持,液氢来说最大的挑战有很多。
为了避免蒸发,又发明了低温压缩的这么一个技术,低温压缩能量密度还比液晶可以做到更高,看压力的状态,但是它也带来其他的问题,又要高压又要低温,对制造成本的技术又带来新的挑战,包括安全性也不太一样,又要低温的安全性,又要高压的安全性,这个前面看挺好,难度很大,未来成本是它最大的一个短板。
在物理里面,材料储氢里面,MOFs是一个有机聚合物,这种材料储氢密度可以做的挺高,最大的挑战是什么一定要结合低温,可以做到16%的比例,但是一个基于它的材料,第二个低温,加了液氮绝热,要转向常温的吸附就来了,常温的吸附出的密度都很低,一般在2%,这是一个很大的挑战。
就有一种碳材料,什么碳,纳米管、多孔维孔碳,活性碳,碳吸附材料,做的指标可以很高,也是在77K下,液氮温度下的材料,容器算下来就下来了,制约性主要在低温下面,成本安全性还可以,碳材料成本还可以,但是这个使用的便捷性是一个很大的问题,所以一直不能用,还有一个技术值得关注我们液体里有机液体储氢,有机液体储氢这些年发展还算比较快的,它其实有两个过程,一个催化加氢,一个催化脱氢,实际上两个反应。
这个里面目前水平可以做到5%以上,甚至国内做到200多以内5%以上,重量密度是挺高,但是这个技术也有很多问题,会带来新的挑战,一个是程度,第二是寿命,系统里也挺复杂,在车载,一般车载我认为这个是用在车上难度很大,但是在特种的应用里,我认为是很有空间的,特别是在长周期长时间的运输和储存,车载里要求太高,又要简单又要响应快,它响应比较慢,有加热系统。
还有金属储氢,金属储氢实际上如果材料储氢的话,我认为如果能金属突破这个成本高能量密度和低温失氢来说,便捷性挺好,往车载应用来讲仍然存在很大的挑战。
其中一个热管理,第二低成本,要和高压竞争,它的成本是一个致命的弱点,每个技术来讲,不能量密度,技术可用材料就2%,加上系统百分之一点几的能量密度,能量密度不高但是体积可以做的很高,压力比较低,安全比较高,我觉得应该在特殊应用里,包括车上也有可能有它的空间,不是一个技术一定要底的,也不是一个技术一定全覆盖,这个里面要注意。
车载属性总结一下,要达到真正车载应用要满足几个条件,第一个要简单,而且要可靠,可靠性要高;第二它的密度要高,无论是体积还是那个重量,相对都要高一点;第三个安全性要高;第四个成本一定要低,而且批量化成本一定要下降,这里我简单排了一个序,有一定倾向性,对现在成熟度来讲优先还是高压,逐渐不同的特殊里面做一些挑战,这个里面提出几个,一个是成熟度,一个是简单、快速响应、低成本,四个关键因素,满足整个目标成本的应用,其实技术满足以后成本是关键,最后一个车乘用车一共才二十万,车载储氢弄个五万、十万这个车没法卖,这是最致命的缺点,不是商品没法竞争,油箱五百块钱,一个车载储氢五万块钱那就麻烦了,汽车也没有希望,还有总体目标设定,简单看得到五年之内,保守一点,五年之内看不到其他车载技术取代掉,还是高压,这是我基本判断,我的报告就到这儿,谢谢大家。
王琨整理
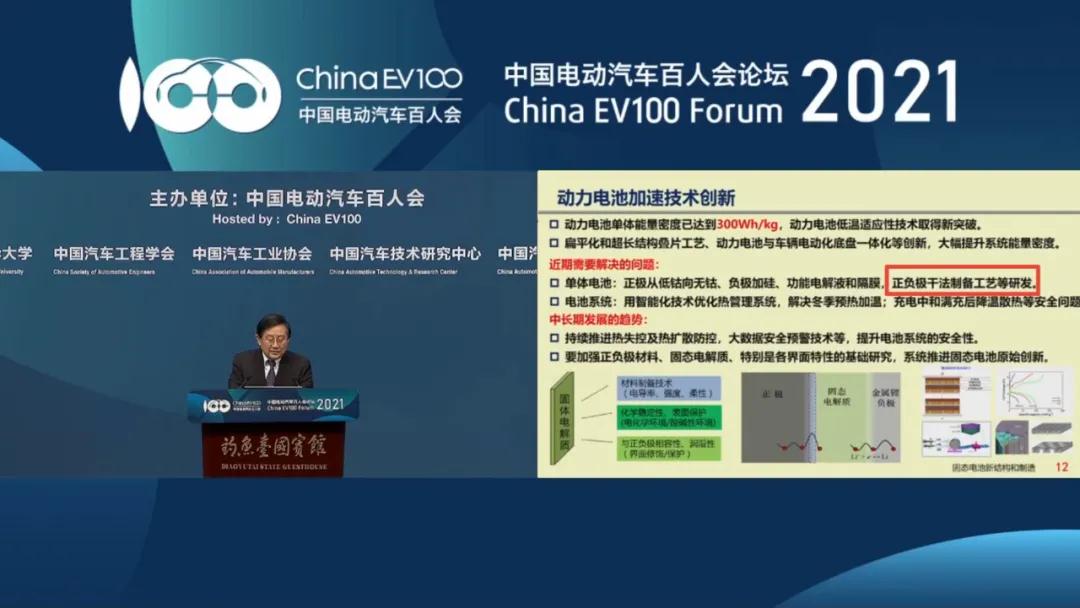
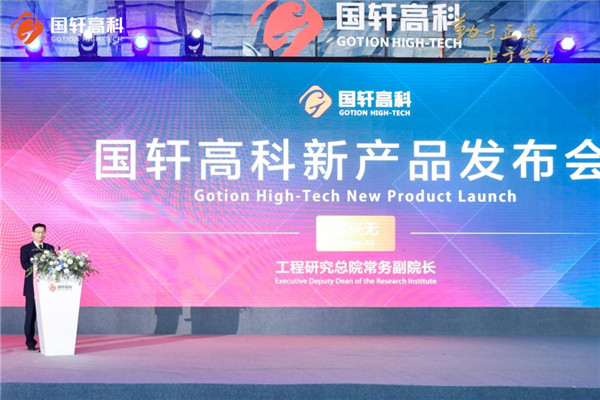
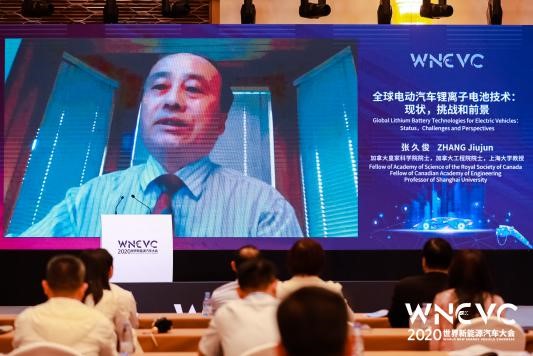
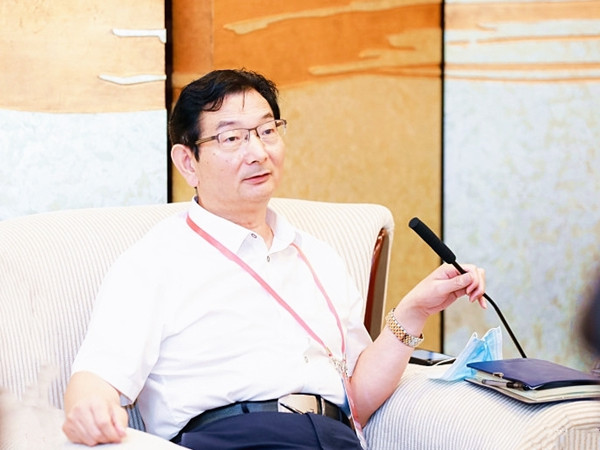
